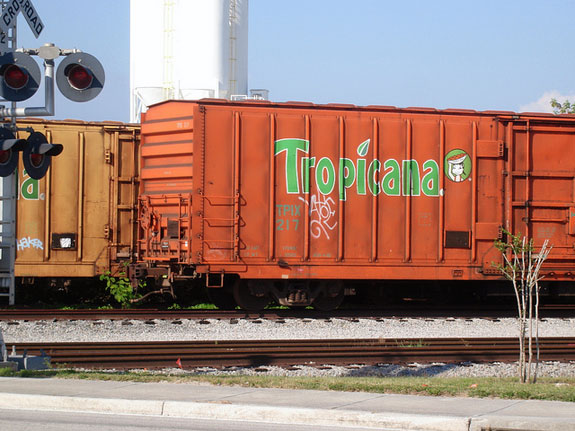
Tropicana’s juice processing plant in Bradenton is a 280-acre facility crossed by railroad lines. The plant is in a federal program designed for safe workplaces. (Photo: Flickr.)
By David Gulliver
Florida Center for Investigative Reporting
At Tropicana’s Bradenton plant, a banner on a fence near the company store reads “Orange you glad you worked safely today.”
And on most days, that’s true — true enough that for 16 years, the orange juice processor has been in a federal program for the safest American workplaces.
For admission into the Voluntary Protection Program, or VPP, workplaces must demonstrate they have fewer accidents and missed-work days than average for their industry. In return, the employers are exempted from the potential annual inspection by the Occupational Safety and Health Administration. Instead, the federal teams visit just once every three years. Studies have found that most, including Tropicana, are indeed safer than their peers.
About This StoryFCIR partnered with the Center for Public Integrity’s iWatch News to examine VPP workplaces. Read iWatch News’ report. Join the ConversationiWatch News reporter Chris Hamby is discussing this investigation on Twitter. Use the hastag #VPPsafety. Watch on TelevisionPBS Need to Know also explored VPP workplaces. Watch an excerpt of the Need to Know report. |
But, according to a new data analysis by the Washington, D.C.-based Center for Public Integrity’s iWatch News, VPP workplaces nationwide also have had at least 80 fatal accidents and hundreds of injuries since 2000.
Texas led the nation, with 20 fatalities and about $44,000 in fines levied by OSHA (which doesn’t include settlements for victims’ families).
In partnership with iWatch News, the Florida Center for Investigative Reporting found the Sunshine State had four fatalities over the same period, tying it for the fourth-highest state total, and just $5,250 in fines.
OSHA data on fatalities can provide an incomplete picture. Two instances cited — a homicide and a traffic accident — were unrelated to workplace safety.
In the other Florida deaths, a Tropicana employee was crushed in a loading dock accident in 2000. OSHA did not cite the company in the incident. The next year, a worker at Georgia-Pacific’s Cross City mill was caught in a conveyor and suffocated.
However, the FCIR/iWatch review also found serious violations at nine workplaces that currently are VPP sites. (OSHA would not confirm or deny they were in VPP when the problems occurred.)
Indeed, OSHA inspections after accidents nationwide have found serious violations of safety laws, and even the companies’ own policies and practices. The workplaces almost always remain in the VPP, even when something has gone terribly wrong — as it has twice at Tropicana since 2000.
Florida is home to 81 workplaces certified for VPP. Bradenton, a city of 54,000 just south of Tampa Bay, is home to two that illustrate both how the program protects employees, and how it can fail them.
Tucked in the midst of middle-class neighborhoods, Blake Medical Center has been in VPP since 2000, and received the program’s “Star” status, recognizing that it meets all requirements, in 2002. OSHA inspectors recertified it with few recommendations in 2002 and 2005, placed it on conditional status in 2008 and then renewed its Star status a year later.
About five miles away sits Tropicana’s sprawling 280-acre plant, crossed by rail lines. The site received its initial VPP approval in 1995. Beverage giant PepsiCo bought Tropicana in 1998, and the plant was awarded Star status in February 2000. Nine months later, an employee was crushed between a truck and loading dock and died at the scene. An OSHA inspection found the company was not at fault and did not issue fines.
But five years later, following a terrible burn accident, OSHA did cite serious violations. In October 2005, two employees were using a highly flammable solvent to clean a compressor in a refrigeration unit, following supervisors’ instructions. A spark from a tool set off an explosion; one worker was burned over nearly two-thirds of his body and another was burned as he tried to save his friend. Both survived.
OSHA’s inspection found eight serious violations and two “willful” violations — the latter meaning that in OSHA’s judgment, the company knew of a dangerous situation and disregarded it. Tropicana paid $164,250 in fines, but remained in the program for model workplaces. (No workers were killed, so that fine is separate from Florida’s $5,250 total for fatal accidents.)
By law, OSHA can request that an employer withdraw from the program, or place it on a conditional approval status. It gave Tropicana conditional status, and returned it to full-fledged Star status a year later. The Government Accountability Office, a federal watchdog agency, found that is the norm: only one in six VPP sites with fatal accidents withdrew from the program, and another one in six received OSHA’s probation.
Meanwhile, though, Tropicana’s accident and illness rates consistently dropped. Its accident reports, audited by OSHA, show those rates falling steadily from 2003 through 2008, before ticking up slightly in 2009. (OSHA inspectors visited the plant for the three-year inspection in mid-May, but its report is not yet public record, and Tropicana declined to release figures.)
Blake’s accident rates have declined from 2007 through 2010, according to its OSHA filings. And in general, VPP sites have maintained clean records. An independent Gallup survey of VPP sites nationwide found that accident rates dropped sharply as workplaces prepare to apply for the program, and continue to drop after certification.
Mark Friend, a professor at Embry-Riddle Aeronautical University and a safety expert who served on Florida’s Task Force on Workplace Safety in 2008, said serious accidents can happen even at companies that make safety a priority.
“Even the VPP companies are going to have something go wrong sometimes,” he said.
In the end, it comes down to the odds: “Buy enough lottery tickets and sooner or later you are going to hit the lottery. Expose yourself to enough risk, which is never completely avoidable, and sooner or later, something happens.”
On the other hand, as one OSHA inspector said, a fatal accident is “the ultimate failure at a VPP site.’’ David Martin, who left OSHA earlier this year after a long career as an inspector, assistant area director and compliance assistance specialist in Pennsylvania, told iWatch News, “The whole concept of the program is to prevent fatalities and injuries.”
Blake and Tropicana have major differences, but both are intricate systems, with hundreds of employees using specialized tools and hazardous substances in a wide array of tasks. The facilities illustrate both the variations in how regulators enforce workplace safety, including the fast-growing VPP, and the difficulty of maintaining safety in a complex work environment.
OSHA Can’t Be Everywhere
The Voluntary Protection Program was born from a pair of beliefs, one ideological and one pragmatic.
It was created in 1982, in the Reagan Administration’s spirit of unfettering businesses from regulation. It also reflected OSHA’s realization that it could not be everywhere: One oft-repeated statistic, circulated by the AFL-CIO labor union and cited by safety expert Friend, notes that at the current numbers of American workplaces and OSHA inspectors, it would take 129 years to visit them all.
Still, the program grew slowly at first. In 1993, it covered just 122 worksites. In 2003, it had grown to 1,039. But then it began to skyrocket, to 2,174 in 2009.
Companies qualify by demonstrating that their accident rates are below industry averages and having no ongoing enforcement actions for safety violations. Meeting all the program requirements, such as documentation of certain safety policies, gets the workplace the Star designation.
But that Star designation is hardly exclusive. About 95 percent of all VPP sites have the Star designation, including both Tropicana and Blake.
A ‘Fluke’ Tragedy and Serious Violations
Tropicana was not always a model for safety. According to OSHA records, the plant was inspected 30 times before 1988, with 250 violations discovered. From 1988 to 1998, after Seagram bought the plant and began gearing up for VPP, violations fell to 12 over 13 inspections.
In an e-mail responding to FCIR’s questions, Tropicana said it invests million of dollars each year in safety, from orientations for new employees to refresher courses for all staff, and in the last three years has made safety-related investments in 20 parts of its operation, including fire systems, lighting and ventilation.
By certifying Tropicana’s VPP status in 1995, OSHA elevated the plant to that small circle of just 267 model workplaces nationwide. As of last month, there were 2,447 such sites nationally, including the Tropicana plants in Bradenton and Fort Pierce.
By 2000, the Bradenton plant had achieved Star status, but just nine months later suffered a tragic accident. Arvid Collier Sr., a 19-year employee, was checking on why a trailer had been left two feet from the loading dock, and walked behind it.
At almost the same instant, another employee returned to the truck and backed it up, crushing Collier, 61, against the dock.
OSHA inspectors saw it as a tragic fluke, where the two employees just missed seeing each other at the trailer. “The fatal accident does not appear to be the result of the company’s failure to establish and/or enforce their own safety and health rules or any appropriate standard,” the inspector wrote.
OSHA did not issue fines but did make several safety recommendations, which Tropicana implemented, according to the case file.
The company sailed through its 2003 VPP inspection, praised for its extensive safety programs. But in 2004, the company had to create a maintenance routine to handle an unforeseen problem.
That December, brine infiltrated the refrigeration system and caused formations of a sludge that collected in various locations. In June 2005, employees began using large quantities of ZEP Brake Wash, a solvent clearly marked as flammable, to clean out both the front and back of compressors.
Rob Hackley and Clifton Van Luven, both mechanics, were cleaning one of the units on October 10, 2005. Around 7:50 p.m., Hackley turned on his electric-powered impact wrench, and a spark ignited the brake wash vapors.
The explosion burned Hackley over 64 percent of his body. Investigators later found remnants of his shirt 26 feet from where he was standing. Van Luven, also burned in the explosion, used his hands to try to put out the flames on Hackley. Another nearby employee sprayed them with a garden hose. Rescue units responded within seven minutes and found Hackley having trouble breathing. They summoned a helicopter, which took him to a trauma center.
OSHA was on the scene the next day, and its investigation found a dozen violations, two of them deemed “willful,” or demonstrating “either an intentional disregard for the requirements of the Act or a plain indifference to employee safety and health.”
The willful findings were based on supervisors’ awareness of unsafe workplace practices persisting for months.
The first stemmed from the fire. Inspectors found that Tropicana had not properly trained employees in using the brake wash solvent as a cleanser. It did not monitor air quality or properly ventilate the work areas. And it did not prohibit ignition sources, like electric tools, from that area.
For the investigation, OSHA interviewed employees, whose comments appear in the heavily redacted 700-plus page report obtained by FCIR.
“(Sr. Supervisor) stated that: ‘We did not consider if the equipment used were designed for a hazardous atmosphere, using flammable material (Brake Wash).’ ”
An unnamed employee said that a supervisor “may not understand the specifics on how the work gets done,” but “as long as they get the job done and under budget, he’s happy.”
The unnamed OSHA reviewer added: “The general consensus of the workforce was that of, ‘If we don’t want to do the work, it may get contracted out.’”
OSHA said the second willful violation was employees being needlessly exposed to 21-foot and 25-foot falls when working in the refrigeration department. According to the report, front-line managers said they “knew it was dangerous but they had to do whatever it took to get the work done because there was no other way to do it.”
The OSHA inspectors wrote: “In general, safety was put aside when major maintenance issues were encountered, and employees were told to ‘throw safety out the window’ and ‘get the work done.’ ”
OSHA recommended several safety improvements and leveled the $164,250 fine. OSHA’s regional administrator met with Tropicana and PepsiCo officials and expressed “extreme concerns,” an OSHA spokesperson, Diana Petterson, said.
Companies regularly appeal and win reductions of OSHA’s findings and associated fines, but in this case they remained unchanged.
Inspectors returned in July 2006, found Tropicana had made the recommended changes, and the agency recertified the plant as a VPP Star site in February 2007.
“The problem had been isolated to the refrigeration unit, and the rest of the plant was in excellent shape,” Petterson said.
Asked how unsafe conditions developed and continued at a company with extensive safety practices, Michael Torres, a spokesperson for Tropicana, provided a company statement: “We look at every inspection as an opportunity to improve our already strong program. If there is an issue, we want to know about it as soon as possible, so we can address it quickly and effectively.”
Expert, Union Chief Cite Safety Hazards
Friend, the Embry-Riddle expert, has consulted with many companies on their safety programs. A strong track record can lead workplaces to develop a false sense of security, he said.
“You see this so often,” he said. “It’s the complacency that occurs. It’s an accident waiting to happen. You do the things again and again and you don’t recognize it as a hazard.”
Robert Tuttle, president of the local Teamsters union chapter representing Tropicana workers, began working at the plant in 1985. He said accidents are more common when employees are shifted out of their normal responsibilities, which is more common as the weak economy has led to staff cuts.
“People are performing a multitude of jobs they haven’t had to do in the past,” he said. For example, a filler operator might have to work cleanup, just 50 feet from his station but a completely different task.
With fewer employees, people are working more hours and overtime, and that also leads to accidents.
“That’s where the fatigue factor comes in,” he said. ”To err is human.”
But he credits the VPP program for changing the culture at the plant and bringing down accidents, illnesses and days of work lost. “I’ve seen definite improvements over the years,” he said. “Since VPP, safety has been pushed to the forefront.”
The praise for VPP is much the same across town at Blake Medical Center.
VPP Credited for Safety at Hospital
Maureen Bennett, a physical therapy technician, has worked at the hospital for 30 years. Earlier in her career, she said, it could be difficult to resolve safety concerns — maintenance staff was always swamped, and sometimes you simply didn’t know whom to ask.
In January, employees were worried about a set of stairs outside the pediatrics and cardiac rehabilitation area. By March, the stairs were replaced with a ramp. The speedy response, she said, was a result of the VPP program. “It’s working wonderfully for us,” she said.
Every department has a member on the hospital’s VPP committee, so employees can take colleagues’ concerns and bring them to management. The committee also does its own quarterly inspections. It creates a mindset that gets employees to work more safely, be it stopping the drips from just-washed food carts to lifting a patient properly.
“If you’re paying attention to safety, you’ll take the extra minute and do things the right way,” said David Matthews, director of plant operations and safety.
It shows up clearly in a rate that VPP tracks, called DART, which measures days away from work, on restricted duty or transferred to other duties. Blake’s three-year average was one-fifth the average for hospitals.
“We have fewer injuries, the injuries are less severe and people get back to work,” Matthews said. That generally translates to lower costs for workmen’s compensation, but Blake did not provide figures.
Having OSHA visit only every three years saves staff time, Matthews said. But the hospital also undergoes top-to-bottom reviews every three years from the Joint Commission, which accredits hospitals, as well as inspections roughly every year from Florida regulators, and occasional inspections from the fire department and building officials.
Together, it means that Blake gets more scrutiny than the typical VPP site — perhaps the best of both worlds, Friend said.
Non-VPP workplaces are eligible for annual inspections, but in practice they are less frequent, he said. Meanwhile, VPP sites must have extensive safety programs, and are guaranteed a visit every three years.
“I understand that they’re escaping, somewhat, from being inspected, but I believe in the end it’s good for the employees,” said Friend. “I believe the bottom line is that companies operate more safely if they are doing so under the VPP umbrella.”
Feds Find Flaws with VPP Program
But two studies by the Government Accountability Office, in 2004 and 2009, found a number of flaws in the VPP program. The latter report found that OSHA resources were stretched to cover the growing number of VPP sites and that poor documentation was allowing workplaces to improperly remain in the program.
Initially, OSHA required VPP applicants to have a three-year average accident rate below industry norms, but in 2008 relaxed that standard. Now, a workplace only had to show its current rate was lower than the industry average for any of the last three years.
In addition to that lowered standard, OSHA also allowed 12 percent of the 184 reviewed workplaces to remain in the program even though their accident rates were above average. In about a third of cases, there were differences between the accident rates provided by the worksite and what VPP reviewers found.
The watchdog agency also looked at 30 workplaces nationwide that had fatal accidents. Five withdrew, and five were placed on conditional status. But 17 were allowed to remain in the VPP program, some as Star sites, until their next review. One worksite, which GAO did not name, had three separate fatalities in the five-year review period.
“Sites that did not meet the definition of the VPP’s Star program ‘to successfully protect employees from fatality, injury and illness” have remained in the program,” the report said.
While OSHA has publicly committed to making the changes GAO recommended, and has acknowledged other problems, about 65 percent of the workplaces with fatal accidents remain in the program, the iWatch News analysis found.
And for some, any improvements will provide little solace.
Rob Hackley, the Tropicana mechanic who was badly burned, is still recovering from the accident. Skin graft surgeries repaired the trauma, but he still receives counseling, his wife, Kim, told iWatch News.
After receiving a settlement from Tropicana, Rob has returned to work, with a new employer. But they still struggle with lingering effects of the fire, and are disappointed with how Tropicana emerged from the investigation.
“The one thing that really still bothers Rob is that they got to keep their ‘Star’ status,” Kim told iWatch News. “If safety really had been a priority, this wouldn’t have happened.”